- Blogs
- All About Valve Jackets and Other Flexible Insulation Covers
All About Valve Jackets and Other Flexible Insulation Covers
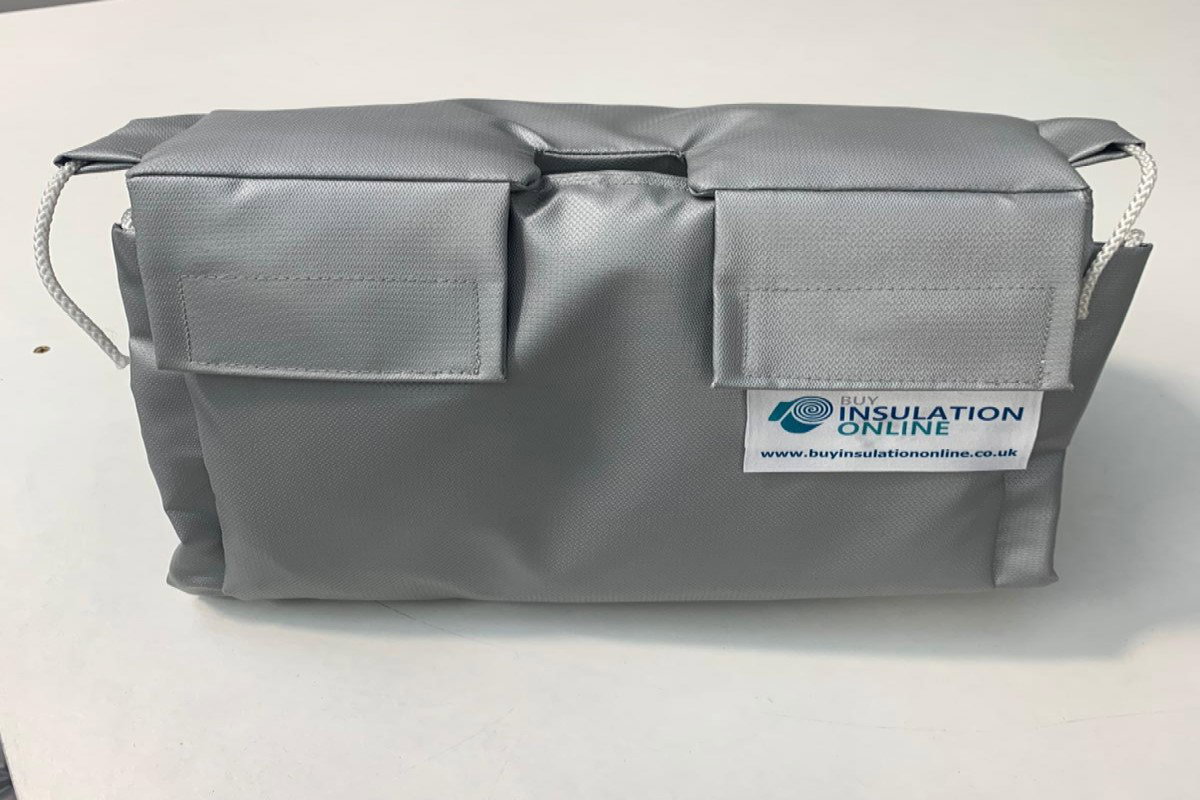
Removable insulation jackets, also known as removable insulation covers, are an innovative solution for insulating pipes, valves, flanges, vessels, and other equipment in industrial facilities.
In this article, we will explore the history of removable insulation jackets, how they work, and the benefits they provide.
History Of Removable Insulation Jackets
Removable insulation jackets, also known as removable insulation covers, were first developed in the United States in the mid-1900s. They were created as a solution to the problem of insulating pipes and equipment in industrial facilities that needed to be frequently accessed for maintenance or repair.
Before the invention of removable insulation jackets, workers had to remove and replace traditional insulation materials every time they needed to access the equipment, which was time-consuming and costly.
With removable insulation jackets, workers can simply remove the jacket and access the equipment, then replace the jacket when they are finished, without having to remove and replace the underlying insulation material. This makes it much easier and more efficient to insulate equipment that needs to be frequently accessed.
Before jackets for valves being invented, most valve bodies were simply left bare.
What are Valve Insulation Jackets?
Pipe insulation jackets are commonly used for protection and to prevent heat loss and gain of valves. Easy to fit and remove, they are the ideal solution for facilities management personnel for maintenance purposes.
Whilst there are numerous types of infill that can be used which can vary greatly depending on the pipework, the insulated filling of the jackets usually comprises fibreglass or Rockwool ductwrap. However, other more exotic materials may be used, like aerogel and AES wool in specialist applications.
An infill of 50mm mineral wool is pretty much standard, which is usually enough to comply with BS5422, the British Standard which sets out how thick pipe insulation should be.
Valve jackets are generally available in one or more layers, that is they are applied in layers on top of each other. In addition, there are several advantages and disadvantages of each system and material.
Valve insulation covers are manufactured for pipework valves that typically require either one or a combination of the following
- Provide Thermal Insulation and Prevent Heat Loss
- Prevent Heat Gain / Freeze protection
- Worker Protection from skin burns
- Acoustic insulation of valves and equipment
- Improve the working environment for employees
- Prevent moisture ingress and associated damage
Valve insulation jackets are designed to be easily removable, which makes them ideal for maintenance and repair applications. As a result, these jackets are also easier to remove than fixed insulation systems or an aluminium valve insulation box for example, and they are less likely to sustain damage due to their flexible nature.
The most common application for an insulation jacket is in HVAC within plant rooms and the like, although they can be used for power stations and petrochemical plants. The valve jackets reduce the ambient room temperature where there is a lot of heat-producing equipment.
They are most commonly used on pipes that are low to medium in temperature however special jackets are made for high-temperature applications which can withstand the heat. In addition to valves, they can also be used on the pipes themselves, cylinders, water tanks, boilers and heat exchangers. They are usually distinct from the type of water tank insulation jackets that you find on the domestic / DIY market and are usually a lot more expensive owing to their quality construction.
The water cylinder tanks that you find in B&Q and Wickes etc are usually nothing more than a bin liner filled with mineral wool insulation. They are great for ensuring the medium temperature is maintained, minimizing heat loss, and preventing condensation on cold pipes. An important aspect of thermal jackets is their ability to protect personnel from burns and potentially harmful heat, resulting in a safer working environment.
They Can Be Up to 70% Faster To Manufacture, Install and Maintain
Carrying out routine maintenance operations on equipment is straightforward using insulation jackets. They have been designed to be rapid to fit or refit, saving time and money. Removable valve covers are vastly superior to other methods of valve and equipment insulation, which are labour intensive and
Why Do You Need to Use Valve Covers?
Valve Jacketing has many benefits. Some of them are mentioned below:
1. Save Energy, Save money and reduce carbon footprint
With the way energy costs are increasing, and the need to reduce the carbon footprint of buildings, jackets save energy on valves that would otherwise be left uncovered. Valve jacket insulation allows you to save energy by thermally insulating the valves properly.
In the below image, you can see the difference in heat given off between a steam pipe valve which is unjacketed, measuring 131 degrees celsius, to the jacketed valve at only 20 degrees celsius. A Huge 110 degrees reduction! The energy savings alone make jackets a good investment, that's without listing the other benefits that they bring too!
These covers are secured with the help of pull cords and straps that pull them tight to valves, closing gaps. They provide good insulation and thus reduce the risk of heat leaking out of your valves. This will save money and by extension, money.
2. Step up from normal lagging.
It can be tedious to remove and re-install hard insulation on valves every time you want to inspect them. It can also damage the valves and the insulation, which makes it useless and not suitable for reuse. It is more cost-efficient to use removable and flexible valve covers rather than having to work and purchase new materials to insulate the valve every time it's worked on.
3. Valve jackets can help you prolong the life of your valves.
Valve covers are used to protect valves from corrosion and other damage. When placed over valves, these jackets provide protection from outside temperatures, direct sunlight, etc. Valve covers make it easy to maintain valves which otherwise would be left open to the elements
Insulating valves with thermal jackets enables you to prevent leaking, rusting, and other problems that could affect them. By preventing big swings in temperature, the valves should not expand and contract so much. This will prevent the stress of expansion on the valve that can cause ruptures and leaking for example Insulated jackets help to protect valves from damage and maintain the performance of the valves for a long time.
4. Saves on Labour Expenses
Flexible and removable jackets enable easy installation and maintenance of all kinds of valves. It is important to periodically inspect and test valves to determine whether they are working properly and if they are wasting energy. Maintaining valves helps in the prevention of damage, leaks, and accidents.
When you remove a valve cover, you can inspect it easily. Just pull the velcro straps that secure the valve and then loosen the cords that attach the valve to the body. Changing valve jackets does not require much effort.
Being easily installed and removed, jackets are better than normal insulation in this regard.
5. Prevent Burns
It is very difficult to prevent workers from being burned by working when hot pipes and valves are uninsulated. Since the valve cover shields the person from the heat, there is no danger of anyone coming in contact with the hot surface of the valve. There are also fewer chances that personnel will burn themselves or be injured while trying to remove the valve cover.
Since valve covers reduce condensation and sweating, they also prevent water droplets from building up underneath the valves on the floor and causing slips or accidents.
Jackets effectively hide sharp edges of applied equipment, thereby making the work environment safer.
6. Safer Environment
It can be exhausting to work with hot pipes and valves. It is inevitable that the area around the valves will be hot as well. You will have less heat generated by heated equipment and pipes by installing covers that provide insulation to these devices. This will enable you to have a cooler working environment. It will help employees to work efficiently in areas that are usually very hot.
You will get a much more comfortable and safer work environment.
7. Stop Condensation
When condensation drips down from pipes and valves, it causes puddles to form in your office. Some people are not aware that water puddles in their workplaces are very small and sometimes they slip and hurt themselves. Flexible insulating covers on valves prevent condensation from forming.
8. They Look Great
Jackets for valves look great and really complement the insulation when correctly fitted and when the right colour is chosen. For the best look, try using one of the combinations below.
- Grey or silver internally with standard foil insulation
- White with Isogenopak Cladding
- Black with PIB rubber weatherproofing finish
- Grey or silver with aluminium cladding finish
As a result, your plant room will look much nicer. You will enjoy working in a more productive environment.
How Are Valve Covers Made?
In general, the valve insulation jackets have one-piece bodies with tubular draw cord channels along their outer margins. Two draw cords extend from each end of the jacket to a correspondingly-positioned removably connected end. Velcro connects the two ends together and any gaps are pulled in by the drawstrings.
Previously, wire was sometimes used to connect and keep the jackets sewn up. However this method of fastening jackets has largely been replaced by velcro straps, pull cords, and belts and buckles. A valve jacket’s fabric cover is its most expensive component. In most cases, the fabric is made of PTFE-coated fibreglass or another high-performance material. An impregnated silicone rubber compound is applied to the surface.
As a result, it is more resistant to abrasion, puncture, and tears. The material is also water and oil-resistant, which is crucial for industrial facilities like petrochemical plants. Some types of valves need to have special shapes cut so the valve jackets can envelop them. A gate valve insulation jacket, for example, has the central body portion elongated, while the opposite end margins are less abruptly curved.
Pipe insulation jackets come in multiple colours but the most common colour is grey. However you can have them made in colours such as black, white and reflective silver, the latter helps even more with reflecting radiant heat away from valves, ideal for cold/chilled water valve applications.
What Thermal Insulation Materials are Used in Valve Jackets?
Fibreglass Ductwrap
When it comes to ductwrap, fibreglass is the most common variety. The best-performing duct insulation roll on the market is Isover Climcover.
With its inherent foil vapour barrier, this strong, flexible and easy-to-handle glass mineral wool duct wrap provides efficient and economic thermal insulation. It’s great as acoustic insulation too. It’s good for use as standard pipe valve insulation, suitable for low to medium temperatures.
Suitable for continuous service temperatures up to 150°C. Fibreglass does not handle moisture or water very well so if that’s a concern you are better off using….
Rockwool Ductwrap
Rockwool Ductwrap is a lightweight, flexible insulation roll, faced with reinforced aluminium foil. It is non-combustible, and non-hydrophobic so is great for high-temperature, and high-moisture environments. Rockwool Ductwrap is recommended for service temperatures of up to 230°C making it more suitable for steam pipe insulation jackets. Rockwool is a little more expensive than fibreglass generally but does have a few advantages that would warrant the extra expense for to use as insulation jacket material.
Aerogel
Hydrophobic Aerogel provides excellent protection against water and is ideal for marine applications. Its thin profile and reduced thickness make it suitable for tight spaces. This insulation also features good acoustic properties, ensuring it is suitable for a variety of industrial applications.
Originally developed by NASA, aerogel insulation was initially used to insulate cryogenic fuel tanks and pipelines. Now, the material has many uses outside the space industry, such as building and refrigeration equipment.
Aerogel provides superior thermal insulation. Its thermal conductivity is as low as 0.015 W m/K
In addition to its excellent thermal insulation qualities, it repels moisture, offering superior protection from corrosion under insulation. Its fire resistant too and can handle high temperatures, another good candidate to be used in steam valve insulation jackets.
So, if you have the budget to spare and are looking for an effective insulator which can be used in tight spaces, then go with an aerogel insulation jacket.
How do I Measure and Order Insulated Valve Jackets?
When ordering from valve insulation jacket suppliers, it’s important to consider the valve type and whether the valve is already wrapped with insulation. This makes a big difference to the shape and size of the jacket itself.
Here are some of the most common pipe insulation jacket types –
- Double Regulating Valve Jacket
- Isolation Valve Jacket
- Check Valve Jacket
- Non-Return Valve Jacket
- 3-Way Valve Jacket
- Butterfly Valve Jacket
- Pressure Reducing Valve Jacket
- Strainer Valve Jacket
- Gate Valve Jacket
- Control Valve Jacket
- Steam Valve Insulation Jacket
- Steam Trap Insulation Jacket
- Globe Valve Insulation Jacket
If you are unsure of what type of valve you have you can send a photo to us at our email address or via WhatsApp in our chat in the below right-hand corner and we can help you identify it.
It is important that if the valve has flanges which you usually find on larger-sized pipework, this needs to be taken into consideration and made note of. Also, make sure you make the manufacturer aware of any kind of test points on the valve that needs constant access.
All valve wraps are made to order so there is no valve, vessel or other H&V equipment that you cannot make bespoke covers for.
The Second thing to consider is the pipe size that the valve is attached to. So if you have an Isolation valve on a 22mm pipe, then naturally you need a 22mm standard valve jacket to fit it.
The third thing to consider is the pipe insulation that may be on the pipe which buts up to either side of the valve. We need to know the thickness of the pipe lagging so we know how big to make the opening on either side of the valve to pull the jackets in tight around the insulation.
You can do this by simply measuring with a tape measure, preferably in millimetres. Finally, we need to know if there is already valve insulation applied to the valve body itself, this will need accounting for as well.
You will usually find chilled water valves to be insulated with duct wrap so we would need to know the thickness of the ductwrap which you can find out if you pull up one corner of the ductwrap and measure it with a tape measure. So to summarise, for a properly fitting valve jacket we would need to know the following–
- Type of Valve
- Is the valve flanged or non-flanged?
- Any Test Points?
- Pipe size / diameter
- Pipe Insulation Thickness
- Is the valve body insulated with duct wrap or any other kind of insulation?
How to Install Valve Jackets
Step 1. Take the cover and wrap it around the valve, and then pull the two ends of the cover tightly tight so that they meet.
Step 2 - Take the velcro flaps that are in the top of each jacket and press them to each other to fasten them in place.
Step 3 - Take the long cords that run along the length of the insulation jacket and tie them tightly, to seal any gaps between the jacket and the valve and the pipe.
Step 4 - Tie the cords together by pulling them tight and pulling them in a tight knot, just like you would tie a pair of shoes.
These heating jackets for pipes that you put on around your valves are very simple to install, and they are very easy to remove also for accessing your valve to make adjustments to the valve, for example.
Application of Insulation Covers in HVAC
Removable insulation jackets can be used to insulate a variety of HVAC (heating, ventilation, and air conditioning) equipment, including vessels, tanks, heat exchangers, air dryers, and filters. These jackets are designed to provide both thermal insulation and acoustic insulation, helping to reduce energy consumption and noise levels in industrial facilities.
Thermal insulation is especially important for HVAC equipment, as it helps to maintain consistent temperatures and prevent heat loss. This can not only improve the efficiency of the equipment, but it can also help to extend its lifespan by reducing the amount of wear and tear it experiences.
Acoustic insulation is also important for HVAC equipment, as it can help to reduce noise levels and create a more comfortable work environment. With a 50mm infill of mineral wool insulation, standard pipe insulation jackets can effectively help prevent noise breakout from valves and associated machinery.
In addition to insulating HVAC equipment, removable insulation jackets can also be used to insulate other elements such as fans and pumps
Acoustic Jackets
Acoustic jackets, also known as soundproofing jackets or noise control jackets, are a type of protective covering that is used to reduce the amount of noise that is emitted by industrial machinery and equipment.
These jackets are made from a variety of sound-absorbing materials like rockwool, polymeric barriers and aerogel. They are designed to cover and enclose the machinery or equipment in order to block or absorb the noise that it produces. They can be designed to provide transmission loss (Rw) of up to 52dB.
A 2.5mm thick, 5kg/m2 polymeric barrier provides an additional boundary layer to provide a barrier to reduce high frequency noise transfer. 10kg/m2 can be used also to provide even more sound attenuation.
Exposure to loud noise can be unpleasant and can cause a variety of negative effects on a person's productivity alongside their health and well-being. Prolonged exposure to loud noise can lead to hearing loss, which can make it difficult for a person to communicate and interact with others, as well as negatively impact their quality of life.
They Reduce health and safety risks and improve the working environment, by insulating key plant and equipment to reduce noise pollution.
Use of Insulation Jackets In Cryogenic Facilities
Cryogenic facilities are used to store and handle materials at extremely low temperatures, typically below -150°C. These materials include liquid gases such as nitrogen, oxygen, and hydrogen, which are used in a variety of industrial and research applications.
Specialist Insulation jackets can be used to protect tanks, pipes, valves and other components from extremely cold temperatures.
They also help keep equipment safe from the elements, such as rain and snow, as well as provide additional safety for personnel working in the facility. Insulation jackets are an essential part of any cryogenic facility, helping to ensure optimal temperature conditions for efficient operation.
High-temperature insulation jackets
High temp jackets are used on turbines, ships and power plants where the temperature of the exhausts can exceed 240°C.
In the context of high temperature insulation jackets, "exhausts" refers to the gases and fumes that are produced by the combustion of fuel in equipment such as boilers, furnaces, and engines for huge ocean-going ships like oil tankers. These exhausts are very hot and can reach temperatures of up to 1200°C or higher, depending on the specific application.
Some examples of equipment and pipes that may be insulated with high temperature insulation jackets include
- Boilers and steam pipes
- Furnaces and kilns
- Industrial ovens and dryers
- Chemical process equipment
- Exhaust pipes and stacks
High temperature insulation jackets are used in a variety of industries, including power generation, chemical processing, manufacturing, and more.
When we are talking about 1200°C, Obviously these sort of temperatures are hazardous to personnel and make working around them extremely uncomfortable if they were otherwise left uncovered. Surrounding mechanical equipment would fail more often if it was constantly exposed to this kind of heat.
They are an important safety measure in these types of facilities, as they can help to prevent fires and protect workers from burns and other injuries. It also makes the working environment tolerable, where it would be near on impossible to work around this equipment without the use of thermally insulated jackets to contain the heat.
Materials used in these types of jackets include fibreglass needlemat, Aerogel and AES Wool.
Medium Temperature applications, Aerogel insulation is used for close tolerance applications up to 650° C with thicknesses from 10mm. For Really High Temperature, AES wool is used for temperatures up to 1100°C with a thickness from 25mm.
Kevlar/Nomex pull cords inside a glass fibre cloth to pull the jackets tight.
Needlemat is often used as an infill material in insulation jackets and blankets, as it provides a high level of thermal insulation and can withstand a wide range of temperatures. It is also resistant to moisture and can help to reduce noise levels.
AES wool, also known as alumino-silicate wool, is a type of high-temperature insulation material made from fibers of alumino-silicate ceramic. It is a strong and durable material that can withstand temperatures of up to 1200°C or higher, depending on the specific application.
AES wool is often used as an infill material in insulation jackets and blankets, as it provides a high level of thermal insulation and can withstand extreme temperatures. It is also resistant to chemical attack and can help to reduce noise levels.
Both needlemat and AES wool are commonly used as infill materials in insulation jackets and blankets, as they provide a high level of insulation and can withstand a high temperatures and harsh operating conditions.
(PFP) Passive Fire Protection Insulation Jackets
PFP stands for "passive fire protection." A PFP insulated jacket is a type of protective covering that is designed to provide passive fire protection to equipment and pipes in industrial and commercial facilities.
PFP insulated jackets are made from fire-resistant materials (such as the ones listed in the high temperature section above) that are designed to withstand high temperatures and slow the spread of fire. They are typically used to insulate and protect equipment and pipes that are located in areas that are at risk of fire, such as power plants, refineries, and chemical plants.
PFP insulated jackets are an important safety measure in these types of facilities, as they can help to prevent fires from spreading and causing damage or injury. They are typically easy to install and remove, and can be customized to fit the specific dimensions and needs of the equipment or pipes being protected.
Overall, the use of PFP insulated jackets can help to improve the safety and reliability of industrial and commercial facilities byreducing the risk of fires and the associated damage and downtime.
Petro-Chemical Valve Insulation Jackets
Valve insulation jackets are used in petrochemical plants, LNG facilities, power plants, chemical plants and boiler rooms.
Jackets can be used for valve assemblies such as ball, globe, butterfly, check, gate, and dual block and bleed (DBB) types. Jackets can be designed to have an easy-to-open inspection hatch for easy valve or actuator maintenance.
Because maintenance shutdowns result in lost revenue for oil and gas companies, using valve jackets can help to reduce the time it takes for each shutdown to turnaround.
Trace Heating Valve Jackets
Insulated valve jackets with integrated trace heating are a type of protective covering for valves that are used in freezing environments such as the Arctic or even Antarctica on research stations. The jackets are made of high performing thermally insulating materials that help to maintain the temperature of the valve and prevent it from freezing.
The jackets also have trace heating elements integrated into them, which use electricity to generate heat and keep the temperature of the valve above freezing. They are fitted with a trace heated cable and thermostat. These jackets are often used in industries such as oil and gas, where valves are exposed to extreme cold temperatures and must be kept operational.
They are also used in other industries where freezing temperatures could cause problems with valve operation, such as power plants and water treatment facilities.
Trace heating jackets provide flow assurance in even the harshest weather conditions by preventing waxes and crystallisation from forming. They ensure flow assurance at water treatment plants, refineries, and offshore facilities during the winter.
Insulated Turbine Covers
Turbine insulated jackets are protective coverings that are used to insulate gas turbine engines. They are designed to help maintain the temperature of the turbine and prevent it from overheating or freezing. The jackets are made of an insulating material that is able to withstand the high temperatures and extreme conditions found in gas turbine engines.
They are usually installed on the outside of the turbine and are used to cover the hot sections of the engine, such as the combustor.
The jackets help to reduce heat loss and improve the overall efficiency of the turbine by keeping the temperature of the engine within the optimal range. Efficiencies of turbines have a direct impact on industrial facilities and power stations. The use of insulation thermal jackets reduces turbine operating costs, improves energy efficiency, protects against fire and reduces noise.
In addition to helping to maintain the temperature of the turbine, the jackets can also protect the engine from damage caused by extreme weather conditions, such as high winds or ice storms.
Common Features Of Most Removable Insulated Jackets
- Provide Thermal Insulation as well as acoustic insulation.
- Most Come Complete With Velcro Straps o alongside pull cords to pull the jackets tight.
- Specific labelling or tagging can be provided for traceability, maintenance, identification and inspection purposes
- Designed to be easily removed and reinstalled during routine maintenance.
Conclusion:
And that’s pretty much it for Insulation Jackets and Valve Covers! Hopefully, this article has provided some valuable insight into what insulation jackets for valves are alongside other types of insulation covers, what their uses are and how to measure them for your projects!
Here at Buy Insulation Online we stock standard flexible valve insulation in a wide range of colours and sizes available for thermal jackets, which comply with BS5422 and feature a silicone-coated glass fibre cloth and 50mm insulation.
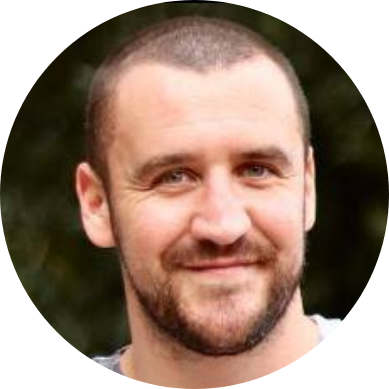
Samuel Hitch
Managing Director
Buy Insulation Online.
Leave A Reply
Your feedback is greatly appreciated, please comment on our content below. Your email address will not be published. Required fields are marked *