- Blogs
- How to install duct insulation?
How to install duct insulation?
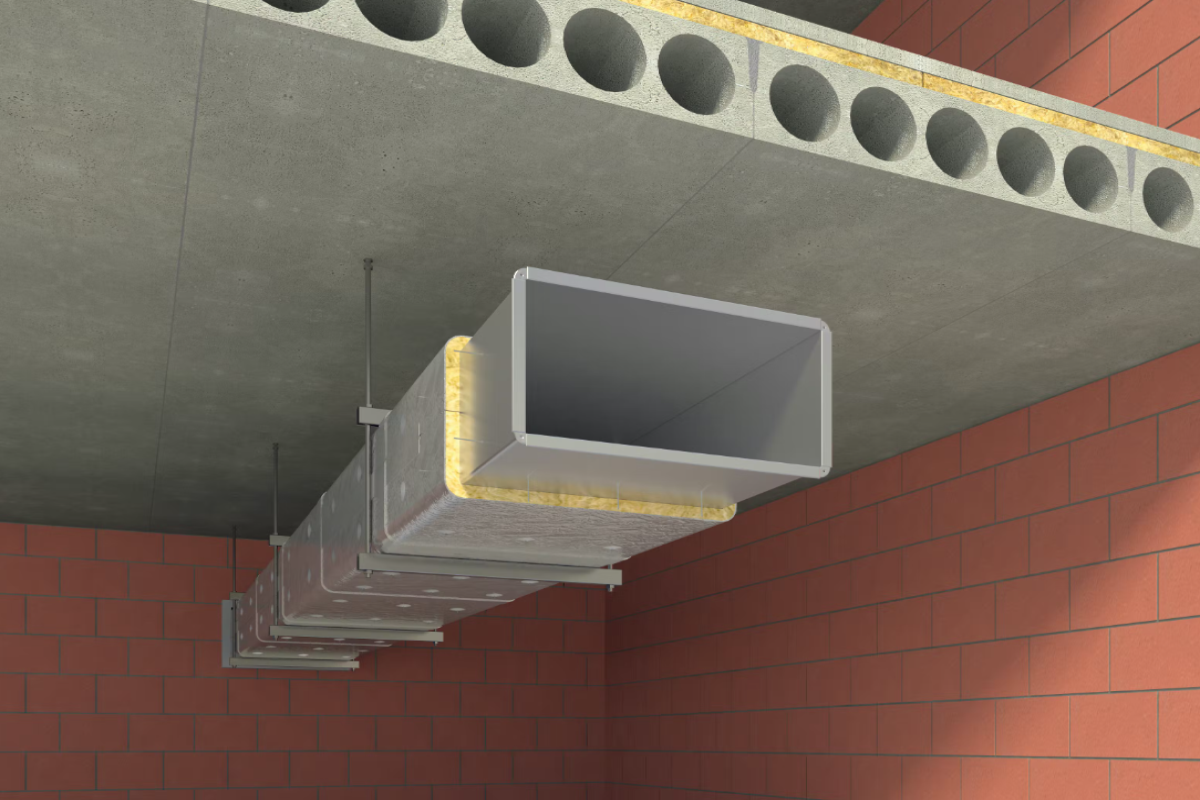
In this blog, we will discuss ductwork, what's its function, various duct insulation materials and specifically, how and why you should insulate ductwork. We will also highlight the different techniques to install duct wrap, foil insulation rolls and ductwork insulation boards.
If you're looking to buy your duct insulation online, we have a huge range of duct lagging hand-picked, just for you. Get duct wrap or duct board, delivered for free where applicable and offset nearly a ton of carbon emissions, through the 3 trees we plant for every order.
We will be using the word lagging throughout the blog also which in the UK is interchangeable with insulation so please keep this in mind.
What does ductwork do?
Ductwork is a network or a system of ducts of varying shapes and sizes that form a part of the building’s HVAC system.
The ductwork of a building ensures thermal comfort and healthy indoor air quality. The supply ducts provide warm or cool conditioned air throughout the facility or home. The return ducts then suck up the stale air which is now too hot/cold from within the rooms and transfer it back to the air handling unit, heat recovery unit or similar.
The return air will then be filtered, re-heated or cooled before being delivered back indoors and the cycle repeats
Some of the air can also be ejected from the facility, depending on the requirements which have been programmed into the system about what internal ambient air conditions are needed.
Occupants of the building can use controls and thermostats to change the temperature within certain zones and rooms, or just across the entire building. Its flexibility and efficiency at evenly warming / cooling an entire space is why it’s so common these days in all types of buildings such as hospitals, schools and are starting to make their way into UK homes through systems such as MVHR (Mechanical Ventilation with Heat Recovery)
What are the benefits of having ducted hvac systems?
Properly installed and maintained ductwork has three main benefits:
For starters, by supplying uniform temperature throughout the building, they maintain an even, comfortable temperature for its inhabitants, whilst eliminating hot and cold patches throughout.
Secondly, it filters out dust particles and other indoor pollution, making the indoor air cleaner and fresher. Special filters can even filter out germs and viruses, including coronaviruses.
Thirdly it is much more effective at heating or cooling a room quickly and evenly than say radiators or split air conditioners. In fact, unless there are split air conditioners in each room which is less efficient, then there is no better way to cool a building than using ductwork.
Ductwork can be hidden in ceilings and walls also, whereas split air conditioners and radiators cannot, meaning more living space and less ugly-looking appliances on show.
The image below is of a huge office building's network of supply and extract insulated ductwork, before it was concealed by a hanging ceiling grid.
Why should you insulate ductwork?
Now you have a general understanding of what ducted ventilation systems are, let's dive into the main topic of this blog, duct insulation, and why it should be installed.
One of the most overlooked factors when ductwork systems are being designed and installed is the duct insulation.
It can be deemed as an unnecessary cost, a burden that is not worth the expense and additional time to install. This could not be further from the truth and it's this short sightedness that can cause big, expensive issues further down the line.
Let's discuss some of the main ways insulating ductwork reaps benefits for building owners and occupiers alike.
Duct insulation is important to maintain a comfortable indoor temperature.
Heating and Cooling air are energy-intensive processes, especially cooling. If an entire system of ductwork is left uninsulated, then through conduction through the walls of the ductwork, heat or coolth will escape from the ducts into uninhabited spaces such as ceiling voids, risers, plant rooms and the like. This is a huge waste of energy.
By the time the air reaches its destination, it has gained or lost a lot of thermal energy, resulting in the room in question not reaching its desired temperature quickly, not at all or in extreme cases, going the opposite direction to the temperature intended.
Obviously, this will be unacceptable for the occupants and will result in complaints which remedying would be expensive (discussed later in this section)
Duct insulation helps soundproof ductwork
Whilst not all duct lagging helps with noise break out, such as rigid foam insulation boards like PIR and phenolic, which actually conduct sound, many insulation products such as the most popular mineral wool ductwraps and insulation duct boards effectively acoustically insulate ductwork, reducing operational noise which in turn makes the workplace / building quieter.
Duct insulation prevents condensation and issues associated with it
When the air inside the ductwork is cooler than the ambient temperature of the air outside the ductwork, it condenses the air touching the ductwork into water droplets. These drops merge together until they begin to become visible on the outside of the ducting. Once the drops get big enough, gravity takes over and the droplets of water begin to drip off the ductwork.
This is known as sweating, and can cause huge amounts of damage to ceilings and other areas in contact with the droplets, resulting in mould and in some cases, the ceiling weakening and collapsing in patches.
By insulating the ductwork, the foil-faced insulation forms a vapour barrier alongside a thermal barrier between the surface of the ductwork and the warmer ambient air, preventing condensation from forming.
Duct insulation makes the building more energy efficient.
Duct insulation saves energy and reduces energy costs by reducing the load on the equipment which heats or cools the building.
As you can see from the graphic to the left here, HVAC equates to over half the energy expenditure of a typical office unit. This number could be even higher if the pipes and ducts are not lagged so it's crucial for facility managers to realise this and action accordingly.
If the ductwork is uninsulated, then heat and coolth is lost through the walls of the ductwork unnecessarily. This means the equipment needs to work harder to replace that heat or coolth than it would otherwise need to if the ductwork was insulated.
Immediately this will cause an uptick in energy consumption by this equipment, but it will also mean it will fail and break down more quickly and more often due to stressing the moving parts out more than would be required if duct lagging was installed.
Therefore, lagging ducts will extend the lifespan of not only ventilation equipment like air handling units, fan coil units, heat recovery units but also heating and cooling plant such as boilers, chillers and heat pumps.
Duct insulation will reduce the carbon footprint of the building.
Like all insulation, duct lagging reduces the amount of energy needed to heat and cool the building. This obviously reduces the carbon footprint of the building and can only be good for the environment. If you or your company has set yourselves to be greener and reduce your impact on the environment, then there's no better way than to install duct insulation.
Duct insulation will be difficult and costly to install once ductwork is concealed.
Unless concealed above suspended ceilings with removable tiles, plasterboard ceilings and walls will have to be torn down to access ductwork once it has been installed. Obviously, this is far from ideal so it is always best to make sure the ductwork is fully insulated and sealed before it is closed up behind plasterboard etc.
What are the different types of duct lagging material available?
Ducts are usually circular, rectangular, square or oval in shape. Flexible insulation materials, like elastomeric foam insulation or mineral wool duct wrap, enable easy installation and effectively insulates awkward corners and bends.
At Buy Insulation Online, we stock foil-faced duct wrap, duct boards and nitrile foam insulation sheets from leading brands. Some of the duct insulation products we store are:
Glass wool foil-faced ductwrap
Glasswool Ductwrap from Isover, is a specially foil insulation roll, designed to provide excellent thermal and acoustic insulation for ductwork. Like all ductwraps, they are highly flexible and can be easily installed, even by non professionals.
Glasswool insulation offers great general fire resistance as well, with the aluminium foil offering Class 0 rating, which helps prevent the spread of fire along with the fire retardant properties of the glasswool insulation itself..
This foil-face insulation roll protects ducts from condensating and the negative effects associated with it . The aluminium foil-facings on the duct wrap also acts as a continuous moisture barrier and protect the ducts from condensation, sweating and other issues.
It tends to be cheaper than Rockwool ductwrap, but doesn't have the same compressive strength and probably not as good for acoustic insulation purposes, albeit not by a huge margin.
Glasswool ductwrap however is probably more environmentally friendly, as it can be made from up to 86% recycled glass, giving things such as glass bottles and windows a second life that will help to reduce carbon emissions over the lifetime of the product.
Having said all that, we also sell Rockwool ductwrap on our site, using either glasswool or rockwool duct wrap will still be a great choice for many.
Mineral rock wool duct board
Foil-faced duct boards from Knauf and Rockwool, are used to insulate rectangular and square-shaped ducts, they cannot be used on circular or oval ductwork unless grooves are cut in them to allow them to bend.
They are known for their A1 fire resistance along with their excellent thermal and acoustic insulation properties.
They tend to be denser, have more compressive strength and rebound which keeps their desired thickness. This means that their thermal conductivity or their K value is kept intact, which might not be the case with ductwrap as installers can tend to pull it too tight, reducing its thickness and therefore its insulative properties.
They also give off less fibres during installation because they are bound with more adhesive than lighter, fluffier foil duct wrap, leading to less irritation.
They can be used to insulate outdoor ducting, and once weatherproofed with either PIB, aluminium cladding or Klasseclad 5 ply aluminium laminate, also known as Ventureclad, and whilst are probably not the best choice for externally insulated ductwork, closed cell insulation is superior in this regard, they offer a more cost-effective solution.
Phenolic duct board / PIR thermaduct foam duct board insulation
Kingspan phenolic foam duct board insulation is probably the best insulator which is widely available, out of all the materials on this list. See the below graphic to see how it stands up against other types of duct lagging.
A close second is PIR or Polyisocyanurate. A lot of people might know PIR by its manufacturer or brand names such as Celotex board, Kingspan Board, Kingspan duct insulation or specifically for ductwork, Thermaduct board.
Whilst not as good an insulator as phenolic, PIR is still excellent in comparison with other duct insulation boards and is also cheaper than phenolic, making it more affordable.
PIR and phenolic have a 90% (or greater) closed-cell structure, which makes them moisture-resistant and non-wicking, making them an excellent choice for external applications in conjunction with a suitable weatherproof cladding like Klasseclad or PIB.
As a result of the factory-applied foil face vapour barrier to products and systems, moisture is effectively prevented from being absorbed into the insulation.
How do you install duct wrap?
The duct wrap installation process is pretty straightforward. We will be discussing the installation of glass mineral wool duct wrap in this part of the blog and then move on to installing duct boards.
Duct wrap is ideal to insulate all types of ductwork, especially circular and oval-shaped ducts but can also be utilised on square and rectangular ductwork.
What are the things you need to do before installing duct wrap?
The materials and tools needed to install duct insulation are;
- Duct Lagging Wrap
- Duct Insulation Board
- 100mm foil tape
- Stick pins
- Insulation wire
- Spray Adhesive for insulation board
- A Tape measure
- A sharp utility knife or a smooth blade, like a fishing knife as linked here.
- Sheath or holder for your knife.
- Tin snips to cut the insulation wire
- Knife Sharpener like this one shown here.
- Face mask / respirator
- Cut resistant gloves
- Disposable coverall or long sleeves / trousers
Professional laggers tend to use the Safeblade knife and holster system as linked here. The rounded edges of the knife mean it's more difficult to stab yourself or others unintentionally (we hope!) and they are relatively inexpensive and can be used for more than just cutting foil insulation.
They also double up nicely as an aluminium foil insulation roll dispenser, by threading the tape through the belt, you can then reel off as much as you like with 2 hands rather than struggling with the roll as so many amatuers tend to do at first.
How to choose the thickness of ductwrap / duct board?
As we are a UK based online insulation store, we will be following the British Standard, BS5422:2009 to choose the thickness of our ductwrap and duct boards. Different codes and standards apply to different regions and countries, but you can be pretty confident British Standards are amongst the best and most rigorous in the world.
One caveat we will make is that the below advice is not meant to be a substitute for proper design calculations which strictly speaking should be made by a competent consultant or building control.
The below advice is general in nature, whilst referring to BS5422 and can be used by the layman to help them choose the correct thickness, but all sorts of factors come into play when selecting the thickness of duct lagging, such as humidity, location of the ductwork, material the ductwork is made out of etc so professional advice should be sought or thorough research should be conducted to allow you to choose the correct thicknesses required.
For the exact thicknesses required, for England & Wales, Refer to TIMSA Guide Section 6.2.5, page 26 & BS 5422: 2009 Tables 12,13 & 14.
Below are snippets from Isover's own foil faced ductwrap data sheet which you can find on our website here.
The first snippet shows you how to choose the right thickness depending on the type of air that's being carried through the duct, to achieve the maximum permissible heat gain or loss. As you can see, 50mm is the specified thickness in most instances. If the ductwork is used for both warm and cold air, you should go with the central, dual-purpose column which states 50mm.
However, if you're just looking to prevent condensation rather than preventing heat gain / loss then the below table details the thickness required.
Generally speaking, condensation prevention on ductwork can usually be achieved with just 25mm thickness, that's if the air within the duct doesn't drop to below 10 degrees which in most cases wouldn’t happen on conditioned air.
However, this is certainly possible with external air during frosty and snowy conditions, which is being sucked in via the fresh air ductwork, which would then require either 40mm or 50mm.
What precautions should I take when lagging ducts?
Fibreglass fibres, whilst deemed by the World Health Organisation to not actually be dangerous, are still harmful to the lungs as they embed in the sides of the airways and irritate them, so make sure you have a good quality respirator on for protection.
Good quality, cut-resistant gloves will help protect your hands from a slip of the knife and slashing your skin.
It's also advisable to wear goggles to protect your eyes and wear long sleeves, trousers or a disposable coverall which will protect you from the itching that happens when your skin comes into contact with fibreglass / rock wool fibres. Another tip is to apply talcum powder on any exposed skin, as it helps prevent the fibres from entering the skin's upper layer, the epidermis.
Having said that, the itching is a temporary side effect, and you can be alleviated with a hot shower at the end of the work day, which opens up the pores allowing the fibres to be released from your skin.
Also when using insulation adhesive, it is recommended that the space be well ventilated as the fumes from the spray may make you feel lightheaded and can permeate dust masks which are not capable of filtering gases and vapours out.
Preparing the work area and ducts ready for insulation.
You should clean the ducts before installing any insulation on them. Simply sweep it clean or wipe it out with a moist cloth. If there is grease on the surface of the duct, this will prevent your insulation stick pins and insulation from adhering to the surface and mechanically fixing the duct insulation. So you can use white spirit or something similar to clean it off.
Also if you have had the ducts freshly installed, make sure the ductwork contractor has performed an air test on them to make sure they are fully sealed, as finding any tiny holes once the duct wrap / duct board has been installed will be impossible without tearing it all off to investigate underneath.
If you are insulating existing ducts you can either ask a contractor to come and air test it, or you can go around yourself and seal all the joints with aluminium foil insulation rolls. This will help keep the system functioning at maximum efficiency.
Your workspace and tools needed for
Always make sure your knife is sharp, mineral wool insulation blunts all types of knives in no time, especially cheaper quality ones. So after every 2 or 3 cuts, it's prudent to run it along with the sharpener like the one linked here once or twice.
It will speed up your cutting by allowing the knife to glide through the duct wrap / duct board rather than having to saw away at it with a blunt blade, which releases more fibres and turns the job into a bit of a nightmare. Having a sharp knife will result in clean cuts rather than jagged, frayed edges which can stand out, especially on duct board edges and corners.
When you are measuring, marking and cutting the insulation, you can lay the duct lagging down on a concrete floor, a large work bench or something you have knocked up for this purpose and mark the measurements to cut with a pen or a marker on the foil-faced side.
Important Note - Do not cut duct wraps or duct boards on a floor or surface, which will either be pierced or damaged itself such as carpet, rubber or wood etc. Only cut on solid, concrete floors or work benches which will not be easily damaged or a meant for this purpose. Exercise caution and common sense in this regard.
Insulation stick pins and spray adhesive
Before we go onto talking about how to cut the insulation and install it onto the duct, you will need to think about where you're placing your insulation stick pins, like the ones shown to the left. They can also be known as self-adhesive insulation hangers.
They are used to keep the insulation snug to the duct, prevent sagging on the bottom and most importantly, will keep the insulation fixed to the duct for years to come.
You should not rely on foil insulation rolls alone to fix duct lagging in place, especially on the sides and the bottoms of the duct. Over time the bond of the foil insulation roll may weaken due to the stresses placed upon it from gravity and also the tautness of the wrap pulled to itself.
In conjunction with insulation pins, you can and should use insulation adhesive, which is basically spray glue like the kind that carpet fitters use for underlay, to not only make your life easier when installing the duct insulation but also physically bond the insulation with the ductwork. Doing all this produces a superior installation that should stand the test of time.
Therefore insulation stick pins, insulation adhesive spray and / or lacing wire should be utilised where necessary.
Stick pins must be placed before the duct insulation is installed, they cannot be installed afterwards. The same goes for the insulation spray adhesive.
How to use insulation stick pins and adhesive for insulation board and wrap
Place the self-adhesive sticky pins on clean and grease free duct faces at every 300mm in a square formation. Stick pins are used only on the sides and the bottom of the ductwork, not on top.
Place the duct wrap over the insulation stick pins and onto the duct, press the duct wrap down slightly. You can bend the pins sticking out of the duct wrap or use a washer to press against the insulation and snip off the excess. Insulation can be further secured using foil tape. We will reiterate this point further along in the blog where relevant
With regards to insulation adhesive., it is important to spray both the duct lagging and the duct face itself, and give the glue a few seconds sink into the ductwrap but do not leave any longer than say 45 seconds as it will begin to lose its tack and will dry.
How to insulate rectangular or square ducts with ductwrap.
Method 1 - wrap around the duct in one continuous piece.
This method describes how to install foil insulation rolls in one piece i.e wrap around the duct and be attached to itself. It's a lot like wrapping a present so if you're a dab hand at wrapping the kids presents at Christmas, wrapping ducts will be a doddle for you.
You will know the thickness of the insulation you will be using, usually either 25mm, 40mm or 50mm so this will need to be taken into account.
Measure and mark the width of the duct times two, the height of the duct times two and the thickness of the insulation times 8 to allow for some overlap so you don't have to pull the insulation too tight, reducing its thickness which will hurt its ability to insulate as advertised.
Basically, if you are using 25mm ductwrap insulation, you want to keep that thickness at 25mm all the way around the duct, not pull it so tight that it reduces the thickness of the ductwrap to 15mm.
So for example, to cut a singular piece of duct wrap to suit a 40cm (Width) x 20cm (Height) rectangular duct using 50mm ductwrap would be cut to these dimensions -
Width x 2 = 80cm
Height x 2 = 40cm
Thickness x 8 = 40cm
W80 + H40 + T40 = 160cm single piece of duct wrap to be cut.
This method works to insulate all rectangular and square ducting.
Now you have your measure, lay the ductwrap on the floor and measure from the start of the roll and mark your measurement with a marker pen, one mark at the top of the edge of the ductwrap , one in the middle and one at the bottom edge of the duct wrap. Then using a straight edge, connect the 3 measurements with your pen, giving you a nice straight guide line to cut down.
After the measurement is marked, you can cut the duct wrap using your knife, trying to keep a nice straight line. There are usually lines on the foil which have the reinforced fibreglass scrim, which you can use as a guide but cannot be relied on completely, hence why it was advised you mark a straight line, unless you are experienced enough to make a straight cut without the line.
Now you have your single piece of insulation, pull a piece of aluminium foil insulation roll off the roll and off the backing paper. Then stick it onto a surface where you can reach it that wont be in the way of the ductwrap installation, you will be needing this piece of tape in a moment. Trust me it is difficult to do this with one hand so you need to try and make your life easy.
Referring to the graphic below, you should try to drape the duct wrap (yellow arrows) over the back edge (shown as blue line) and down the back of the duct, so the leading edge of the ductwrap sits flush with the top corner which is closest and facing you (shown as red line). Get the piece of foil tape you just pulled off and use it to tape down the edge of the ductwrap onto the duct itself along the corner facing you / red line. Rub the foil insulation roll down properly.
This will now secure the ductwrap in place so it doesn't drop down the other side, freeing your hands to get the other edge of the wrap to pull around from underneath. Pull another piece of foil insulation roll off the backing paper again and place it within reach on a surface near you.
Then grab the edge of the ductwrap which is draping down the other side, pull it round underneath, pierce any insulation pins that you placed previously through the wrap and bend them over or use washers to secure the bottom in place. Take care to remove any sagging, the ductwrap must be snug with the bottom of the duct.
Finally, get the piece of foil tape you left within reach and put it on the ductwrap edge that's hanging free, then with both hands pull the wrap up the side and tape it to itself. Do not pull it too tight and reduce the thickness of the duct wrap, it will reduce its ability to insulate the duct properly. Foil insulation roll the entire joint.
Move on to the next piece and repeat the process. Then foil tape the circumferential joints and always rub the tape down properly along all joints, preferably with a plastic spatula or similar like the one shown to the left here. It makes the installation look alot more professional rather than looking like some kitchen tinfoil crinkled up on all the joints.
Mechanically securing duct wrap in place with insulation wires
After you have taped up the lagging, you can further mechanically secure it around the duct using insulation wire in addition to any insulation stick pins that you may have used.
Insulation wire is basically galvanised steel wire with a thickness of 1mm. It's strong, rust resistant and easy to install. You just need a pair of metal shears / snips to cut the wire when needed. You can also buy a tie wire reel like this one linked here, to reel the wire onto which you can then dispense easily. Otherwise, you should wrap the wire around a rolled-up piece of cardboard or similar so it doesn't get twisted and tangled which can happen if you try and pull it straight off the roll.
To do so, throw the wire around the duct lagging, and pull it back to yourself. If it's large ductwork you may need someone to pass it to you or use a stick to hook it back to yourself.
Then get this end and loop it around the other end of the lacing wire, which should now mean you can pull on the wire so it starts to tighten onto the duct wrap.
Don't over-tighten the wire, remember it's just there to secure the lagging, we want to keep the insulation thickness if you remember.
Once you have tightened it sufficiently, snip off about 50mm from the loop, bend it away from the loop so it doesn't begin to loosen off and push it to the insulation and tape the puncture over, using foil insulation roll.
Insulation wires should be placed at a distance of roughly 400mm from the ends of each segment of duct wrap. This method can be used to insulate circular, oval, rectangular and square ductwork.
The photo below shows a project where lacing wires are placed every 400mm on both rectangular and circular ductwork along with insulation stick pins on the underside of all the square ductwork. It also utilised the method previously described, using one singular piece of wrap rather than the next method which involved lagging each side of the duct separately.
Note how ductwork identification triangles are placed every 3m on the underside of the ducts, for ease of identifying which duct does what for maintenance purposes. We will go into more detail about these at the end of the article.
Method 2 - insulate each face of the duct separately
Alternatively, you can simply insulate each side of the duct separately. It must be said that this method is slower than the previous one and also means there will be more joints to tape, so more aluminium foil insulation rolls will be used as a result.
However this method may be the only one feasible in certain situations such as where there is limited access, the ducts are tight to walls and other services etc where its impossible to pass the ductwrap back round to yourself. Its also required to do this on rectangular / square duct elbows, where you cannot wrap the duct all the way around because the next piece of duct gets in the way.
First measure the width of the duct, mark it on the duct wrap and cut the section out. Then mark the height plus twice the thickness of the duct wrap and cut out that section separately. You need to allow for the thickness twice so it over laps the tops and bottoms accordingly.
You will need to use more stick pins and insulation adhesive for this method, to mechanically secure each face of the ductwrap pieces in place.
How to i
nsulate circular ductwork:
To get the desired length of ductwrap for circular or oval ductwork we can either use a little bit of high school math to calculate the circumference and pi(π) or simply throw the tape measure around the duct and physically measure the circumference and account for the thickness of the duct wrap.
First, let's calculate the circumference using Pi and then you will understand why you need to account for the thickness of the duct insulation.
So let's suppose we want to insulate a 100mm diameter duct with 50mm thick duct wrap as an example.
100mm diameter duct + (50mm insulation x 2) = 200mm outside diameter of duct insulation as in graphic to the right here. You can convert the MM into CM if you find that easier to work with.
0.2 x 3.14 (Pi) = 0.628 = 628mm circumference, or 62.8cm. 62.8cm + 50mm lap = 63.3 cm length of insulation required to go around the circumference of the duct.
As you can see, the ductwrap thickness is what determines the outside diameter, an therefore the circumference of the ductwrap piece that needs to be cut.
Knowing this, you can therefore throw the foil tape around the duct and back to yourself to figure out the circumference of the duct alone without having to use the calculations. Once you have the duct circumference, you will need to add on more to account for the lagging. So for 50mm you would need to add on around 32cm based on our previous example because…
The circumference of a 100mm dia duct is = 314mm which is exactly half our example which accounted for the ductwrap. Hence why the extra 320mm is required to enable the duct lagging to go all the way around the duct and come back to meet itself so you can tape it together with a little bit of overlap whilst not having to pull it overly taut which as we discussed previously will hurt its thermal conductivity and mean it is under strain and more likely to spring and peel off the ductwork over time.
Now you have the measurement, cut the insulation to the desired size. A lot of the instructions we gave with rectangular ducting apply the same here.
So throw the insulation over the duct and drape it down the other side and tape it to the duct itself so it hangs free without falling to the floor. Pull off some foil insulation roll, attach it to the other end and pull it back round and secure the wrap to itself using.
You can further secure the duct wrap using lacing wire every 400mm from and complete the installation using duct triangles. Please note, insulation stick pins are not used on circular ducts as they will not adhere to the arced surface.
How to insulate spiral duct bends:
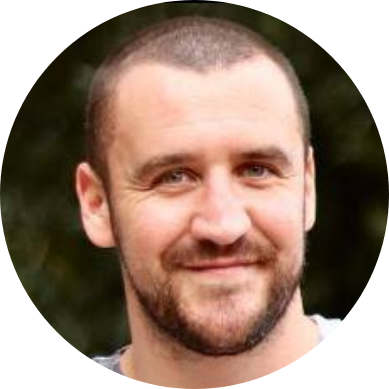
Samuel Hitch
Managing Director
Buy Insulation Online.
Leave A Reply
Your feedback is greatly appreciated, please comment on our content below. Your email address will not be published. Required fields are marked *