- Blogs
- Underground Pipe Insulation: A Comprehensive Guide for UK Applications
Underground Pipe Insulation: A Comprehensive Guide for UK Applications
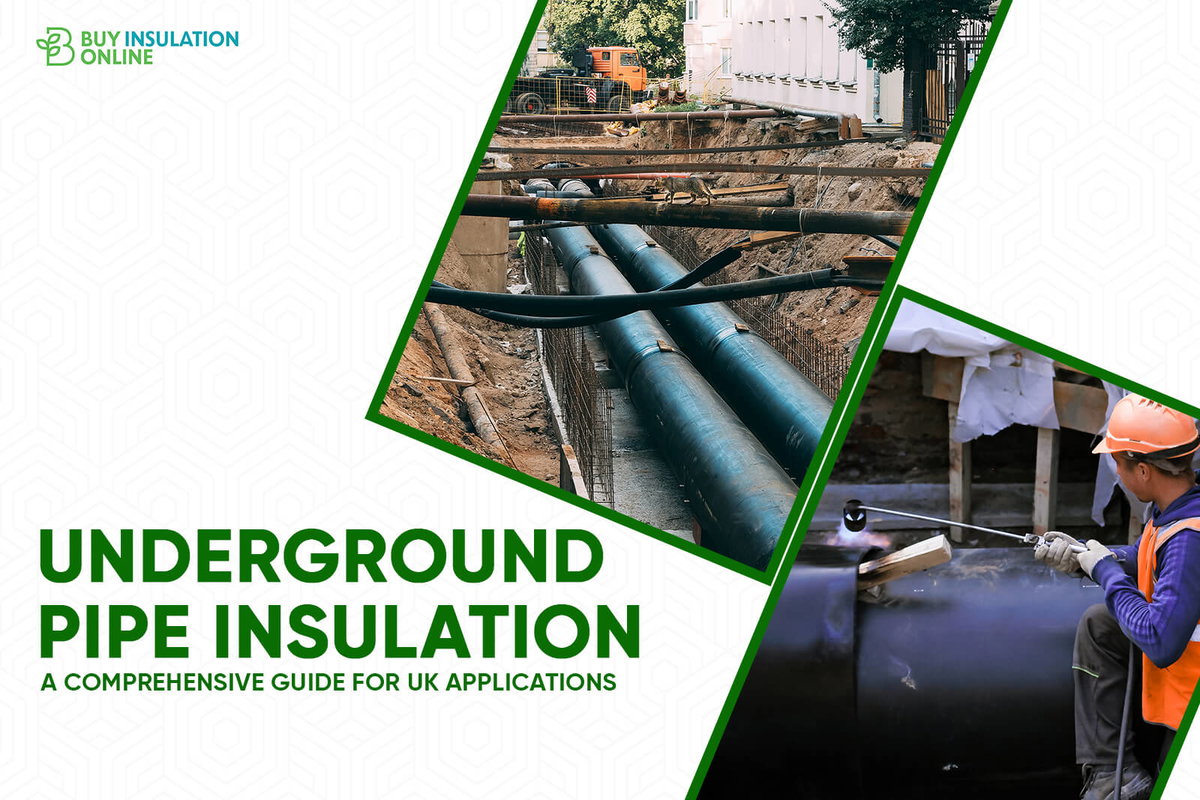
Underground pipe insulation plays a critical role in protecting pipe systems, reducing energy consumption, and ensuring long-term infrastructure reliability. For installations throughout the UK, proper insulation is not merely beneficial but often mandatory under current building regulations.
This guide explores the materials, techniques, and regulations surrounding underground pipe insulation for UK applications while providing valuable insights for international readers.
Key Points Summary / TLDR
Underground pipe insulation is vital in the UK for energy efficiency, preventing frozen pipes, and meeting regulations. Common materials include polyethylene, elastomeric, and polyurethane foams, as well as foamglass. UK standards like BS 5422 and Building Regulations Part L dictate requirements. Proper installation and protection are key to long-term benefits like reduced energy bills and avoiding costly repairs.
What is underground pipe lagging?
Underground pipe lagging is a critical aspect of infrastructure in the United Kingdom, serving a multitude of purposes that extend far beyond the basic prevention of freezing. In the UK's diverse climate, effective insulation plays a pivotal role in bolstering energy efficiency, safeguarding the integrity of essential water and heating systems, and ensuring adherence to stringent building regulations and water authority standards. The benefits of properly insulating buried pipes are substantial and far-reaching.
One of the primary advantages is the significant improvement in energy efficiency. By effectively minimizing heat loss from heating systems and reducing heat gain in cooling systems, insulation directly contributes to lower energy consumption and, consequently, reduced energy bills for both domestic and commercial users. Furthermore, in the UK's often cold winters, insulation provides vital frost protection, preventing water within pipes from freezing and potentially causing costly and disruptive bursts.
Compliance with the UK's building standards and the specific requirements set forth by local water authorities is another crucial benefit of appropriate underground pipe insulation. Additionally, insulation plays a key role in preventing condensation on cold water pipes, which can lead to corrosion of the pipe material and the growth of harmful mould. Finally, a less commonly recognised benefit is the reduction of noise generated by water flowing through pipes, contributing to a more comfortable environment. The multifaceted advantages of underground pipe insulation underscore its importance in creating efficient, reliable, and compliant infrastructure across the UK.
Materials Used for Underground Pipe Insulation
When selecting insulation materials for underground pipe applications, several factors must be considered including thermal performance, water resistance, compressive strength, and longevity. The UK market offers various solutions suited to different applications.
Foam-Based Insulation
Foam pipe insulation represents one of the most common solutions for underground applications. Typically made from polyethylene or elastomeric materials, these products offer flexibility and lightweight characteristics that conform effectively to pipe shapes.
As noted by industry specialists, "Foam pipe insulation can be used underground, but it needs to be properly installed and protected from moisture, rodents, and other potential hazards". These insulation products come in various forms including pre-slit tubes, rolls, and sheets that can be cut to fit specific pipe dimensions.
Important: All compressible materials like polyethylene and elastomeric foam must be protected with either insulated ducting or aluminium cladding to prevent them from being crushed by soil pressure, which would compromise their insulating properties.
Key benefits of foam-based insulation include:
-
Cost-effectiveness compared to many alternatives
-
Excellent thermal resistance properties
-
Relatively easy installation process
-
Flexibility in accommodating different pipe diameters
However, when using foam insulation underground, proper moisture protection is essential. Most foam products require additional waterproofing measures to prevent degradation in wet soil conditions.
Polyethylene Foam
Is a flexible, lightweight, and cost-effective option that provides good insulation against both cold and heat while offering decent resistance to condensation. Popular UK brands include Climaflex and Armacell Tubolit. While versatile for indoor and some outdoor uses, specific types are designed for underground applications with enhanced water resistance.
Elastomeric Foam
Often made from synthetic rubber, offers excellent flexibility with a spongy texture that proves highly effective at preventing moisture penetration. Armaflex is a widely recognised brand in this category. Due to its high moisture resistance, elastomeric foam is frequently used in areas prone to condensation and typically achieves a Class O fire rating.
Phenolic Foam
This material combines excellent thermal performance with inherent fire resistance, making it a high-performing insulation material. However, it tends to be more expensive and can be brittle, meaning it will probably crack and break under pressure. For underground use, phenolic foam necessitates waterproof and mechanical damage protection to maintain its integrity. Kingspan Kooltherm is a prominent brand in the UK offering phenolic foam pipe insulation.
Polyurethane (PUR) Insulation
Polyurethane foam provides excellent thermal insulation and structural rigidity, making it a strong contender for underground applications, particularly within pre-insulated pipe systems. While potentially vulnerable to moisture in direct burial scenarios without proper protection, it offers good resistance to chemicals, enhancing its suitability for certain underground environments.
PUR insulation is commonly used in district heating networks and offers thermal conductivity values as low as 0.023–0.027 W/m·K, making it highly efficient for minimising heat loss. It can be manufactured in both rigid and flexible forms, with the rigid version being particularly suitable for pre-insulated pipe systems.
Foamglass Insulation for Underground Pipes in the UK
Foamglass insulation represents a high-performance solution for underground pipe insulation in the UK, particularly in demanding applications where moisture resistance and structural integrity are paramount. This unique material is composed entirely of glass, making it inorganic and free from any binders or fillers.
A key characteristic of foamglass is its complete impermeability to moisture, whether in liquid or vapor form, ensuring that its insulation properties remain unaffected by damp underground conditions. It is also unaffected by soil acids and is chemically inert, contributing to its long-term durability in buried environments. Furthermore, foamglass is non-combustible, achieving an A1 fire rating, which is a significant safety advantage. Its high compressive strength allows for direct burial of pipes without the need for additional protective tunnels, simplifying installation and reducing costs.
Foamglass is also dimensionally stable, meaning it does not shrink, swell, or warp over time, and it is resistant to infestation by insects and rodents, ensuring the longevity of the insulation system. The service temperature range of foamglass is exceptionally wide, typically spanning from cryogenic temperatures up to high temperatures such as 482°C (900°F), making it suitable for a variety of underground pipe applications.
In the UK context, foamglass is particularly well-suited for the direct burial of hot water, steam, and chilled water pipes due to its inherent resistance to moisture and its ability to withstand the compressive forces of the soil. Its impermeability makes it an excellent choice for areas with high water tables, where other insulation materials might degrade over time due to moisture absorption.
It must be noted foamglass is not easy to install and should be left to a specialist thermal insulation contractor to undertake installation.
The advantages of foamglass for underground pipe insulation include:
-
Exceptional water resistance without additional barriers
-
Non-combustible properties (Euroclass A1 rated)
-
Dimensional stability preventing water leakage
-
Ability to bear heavy loads without deformation
-
Resistance to rodent and insect damage
-
Long service life with minimal degradation
-
Service temperature range from cryogenic to 482°C (900°F)
Foamglass is particularly valuable in high-groundwater areas or where pipes may be subjected to significant external pressures. Its closed-cell structure prevents water absorption, making it ideal for installations below the water table.
Can Mineral Wool and Fibreglass to insulate underground pipes?
Mineral Wool, encompassing products like Rockwool and stone wool, offers a combination of fire resistance, sound absorption, and the ability to withstand high temperatures, up to 700°C. It is available in various forms, including blankets, boards, and specifically designed pipe wraps.
To enhance moisture resistance, mineral wool insulation is often faced with foil. For outdoor underground applications, an additional protective covering sheet known as Polyisobutylene (PIB) may be required. Rockwool Rocklap is a specific mineral wool pipe insulation product widely available in the UK.
Fibreglass insulation provides good acoustic performance and fire resistance. It is available as duct wrap, preformed pipe insulation sections, and flexible blankets. However, fiberglass is not inherently waterproof and requires additional protection against moisture ingress for underground applications. Isover Climpipe is a recognized brand of fiberglass pipe insulation in the UK market.
Both mineral wool and fiberglass are compressible materials that require both protective ducting or aluminium cladding and a waterproof cladding when used underground to prevent crushing from soil pressure.
This makes them unsuitable for use as underground pipe insulation in most cases.
Other Specialised Materials
Calcium Silicate is a rigid insulation material known for its ability to withstand very high temperatures, up to 1200°F, and its fireproof properties. It exhibits low thermal conductivity and is primarily used for insulating high-temperature pipes in industrial settings.
Aerogel insulation, known for its extremely low thermal conductivity, is typically reserved for niche applications such as cryogenic insulation.
Material | Key Properties for Underground Use | Typical Applications | Suitable for use as underground pipe lagging? | Common Brands in the UK |
Polyethylene Foam | Good moisture resistance, cost-effective, lightweight | General underground pipes, water service lines | Yes with cladding | Climaflex, Armacell Tubolit |
Elastomeric Foam | Excellent moisture resistance, flexible | General underground pipes, areas prone to condensation | Yes with PVC coating or cladding | Armaflex EVO Tuffcoat, Stornch PVC Coated |
Polyurethane Foam | Excellent thermal insulation, rigid or flexible | Pre-insulated pipes, general underground pipes | Yes with PVC coating or cladding | |
Phenolic Foam | High thermal performance, requires waterproofing underground | Limited direct underground use, often in protected ducting | No unless with both waterproof and moisture proof cladding | Kingspan Kooltherm |
Mineral Wool | Fire resistant, good thermal insulation, often foil-faced | General underground pipes with additional protection, industrial applications | No unless with both waterproof and moisture proof cladding | Rockwool, Rockwool Rocklap |
Fibreglass | Good thermal insulation, requires protection from moisture | General underground pipes with ducting or vapor barrier | No unless with both waterproof and moisture proof cladding | Isover Climpipe |
Calcium Silicate | High-temperature resistance, rigid, requires protection from moisture for underground use | High-temperature industrial pipes, limited direct underground use without protection | Yes | |
Foamglass | Impermeable to moisture, high compressive strength, chemically inert, non-combustible | Direct burial of hot, cold, and steam pipes, high water table areas | Yes | FOAMGLAS® |
Common Cladding Materials for Underground Pipes
Insulating underground pipes is essential for efficiency and preventing issues like heat loss or freezing. However, the underground environment demands a robust protective layer, or cladding, to shield the insulation from moisture and mechanical damage.
Aluminium Cladding
Aluminium is a popular choice due to its good moisture resistance and durability. It offers effective protection against water ingress and mechanical damage, even at relatively low thicknesses. Aluminium sheets are generally cost-effective and can last for many years. Installation involves overlapping and securing with rivets and tape.
Polyisobutylene (PIB) Cladding
PIB is a synthetic rubber known for its excellent waterproofing capabilities. It provides a strong barrier against water and vapour, crucial for underground applications. PIB is also tough, durable, and flexible, offering good resistance to mechanical damage.
PVC Cladding
PVC can offer some water resistance and is often used for pipe insulation. While it might be suitable for less demanding underground conditions, its mechanical strength may not be as high as metal options.
VentureClad and ProClad
VentureClad is a well-known thin, self-adhesive cladding with a stucco embossed pattern that helps conceal imperfections. ProClad is another self-adhesive option. These types of cladding offer ease of installation and good protection.
Specialized Cladding for Underground
For direct burial, specialized systems like Armaflex Tuffcoat are available. This insulation has a built-in self-seal plastic coating for easy installation and protection against the elements. FOAMGLAS® insulation, when used with PITTWRAP® jacketing, also provides a robust, waterproof solution for direct burial, though PITTWRAP is less common in the UK.
Cladding Material | Water Resistance | Mechanical Strength | Flexibility | Cost-Effectiveness | Estimated Lifespan | Best Suited For |
Aluminium | Medium, only as good as the joints are sealed. | High | Moderate | High | 20-30+ years | General underground, areas with mechanical stress |
PIB (Polyisobutylene) | Exceptional when joints are sealed properly | Medium. Easily Puntcured | High | High | 10-20 years | High water table, areas needing flexibility |
PVC | Moderate to Good when joints are sealed properly | Moderate | High | High | Varies | Less demanding underground applications |
VentureClad/ProClad | Good when joints are sealed properly | High | High | Moderate | Varies | General underground, ease of installation |
Armaflex Tuffcoat | Excellent | Good | High | Moderate | Long-term | Direct burial, waterproof insulation |
Key Considerations
When choosing cladding, consider the water table level, potential for mechanical stress, ease of installation, budget, and compatibility with the insulation material. For high water tables, PIB or specialized direct burial products are ideal. In areas with potential for damage, aluminium offers excellent protection.
Installation Tips
Ensure proper sealing and overlapping during installation to prevent water ingress. It's also important to seal all joints and seams with appropriate sealants to create a continuous barrier against moisture. Remove sharp objects from the trench before burial to avoid damaging the cladding. Consider using a layer of sand around the pipe to provide additional protection against punctures from rocks or debris in the soil.
Pre Insulated Pipes for Underground Use in the UK Market
Pre-insulated pipes represent an advanced solution for underground services in the UK, offering a comprehensive approach to insulation and protection.
These systems typically comprise a carrier pipe, which can be made of steel or plastic materials like PEX (cross-linked polyethylene), surrounded by an insulation layer, often made of polyurethane foam, and encased within a durable protective outer casing, commonly made of high-density polyethylene (HDPE) or glass-reinforced plastic (GRP).
The adoption of preinsulated pipes brings numerous benefits to underground infrastructure projects. Their pre-assembled nature leads to faster and easier installation, significantly reducing the amount of on-site labour required. The use of flexible PEX pipes, often supplied in coils, further simplifies the installation process by minimizing the need for
joints and allowing for easier navigation around underground obstacles. A key advantage of pre-insulated pipes is the consistently high level of thermal insulation achieved through the factory-applied insulation layer, which minimizes heat loss and enhances energy efficiency.
Some advanced pre-insulated pipes even offer exceptionally low thermal conductivity (lambda values), further reducing heat loss. The robust outer casing provides enhanced durability and protection to both the carrier pipe and the insulation layer against mechanical damage, corrosion, and the ingress of moisture from the surrounding soil. The HDPE outer casing, in particular, offers excellent protection against these underground elements. The inherent flexibility of many pre-insulated pipe systems allows for easier design and installation, accommodating complex underground layouts and reducing the need for numerous fittings. Finally, the high-quality materials and construction of pre-insulated pipes often contribute to a longer service life compared to traditional insulation methods.
Preinsulated pipes find extensive applications in various underground services within the UK. They are a cornerstone of efficient district heating systems, facilitating the distribution of hot water from a central source to multiple buildings. Their use is also prevalent in ground source heat pump installations, supporting sustainable heating solutions. Additionally, pre-insulated pipes are employed in chilled water systems for efficient cooling of large buildings , and they can be utilized for the underground transport of a variety of other fluids requiring temperature control.
Installation Considerations
When installing pre insulated pipe systems underground, proper trenching and bedding procedures are essential. Industry guidelines specify that "a trench shall be provided so as to enable pipe placement... with at least 10 cm pipe bedding made of sand free of stones, debris and sharp-edged objects".
Key installation considerations include:
-
Ensuring proper trench dimensions (width and depth)
-
Providing suitable sand bedding and backfill
-
Managing pipe expansion and contraction
-
Proper jointing and field insulation of connections
-
Protection at building entry points
For house connections, there are typically three methods for introducing pre-insulated pipes through walls:
-
Straight lead-in through the base
-
Tilted bore in the base
-
External lead-in through the wall, covered by a cabinet
Proper installation ensures system longevity while maintaining thermal performance throughout the service life.
Best Practices for Installation, Maintenance, and Protection
Ensuring the long-term efficiency and reliability of underground pipe insulation in the UK requires adherence to best practices throughout the installation, maintenance, and protection phases.
Proper installation is paramount. The process should begin with careful preparation of the trench, ensuring adequate depth to fall below the frost line and sufficient width to accommodate the pipes and insulation. Any sharp objects within the trench should be removed to prevent damage to the pipes or insulation. Pipes should be laid securely and tested to ensure they are leak-free before insulation is applied. When wrapping pipes with insulation, it is crucial to ensure complete coverage without any gaps. Seams and joints in the insulation should be meticulously sealed using appropriate adhesives or tapes to create a continuous thermal barrier. For foam insulation, especially in damp underground conditions, protecting the insulation with a vapor barrier is essential to prevent moisture penetration. In areas where rodents are a concern, considering a rodent-proof barrier such as a metal mesh around the insulation can be beneficial. When backfilling the trench, care should be taken to avoid using sharp or heavy materials that could puncture or compress the insulation. The backfill material should be tamped down to eliminate air pockets. Using a layer of sand or pea shingle around the pipe can provide additional bedding and protection. For pre-insulated pipe systems, it is vital to follow the manufacturer's instructions for jointing and sealing the pipe sections. Using shrink end caps at underground connections is a recommended practice to prevent water ingress into the insulation.
Maintenance of underground pipe insulation is challenging due to the inaccessibility of buried systems. Therefore, the focus should be on preventative measures and robust initial installation. Regular inspections of any exposed sections of the pipework, such as where they enter or exit buildings, can help identify potential issues early. If any signs of wear, damage, or compromised insulation are detected, they should be addressed promptly by patching holes, resealing joints, or replacing damaged sections. For the buried sections, the quality of the initial installation and the durability of the materials used are critical in minimizing the need for future repairs, which would likely involve excavation.
Protecting underground pipe insulation from moisture, rodents, and soil conditions is crucial for its longevity and performance. Utilizing closed-cell insulation materials with inherent water resistance is a primary defense against moisture ingress. For insulation materials that are less water-resistant, employing vapor barriers and waterproof jacketing can provide the necessary protection. Implementing rodent-proof barriers can prevent damage from pests. Ensuring proper bedding and backfilling around the insulated pipes helps to prevent mechanical damage from the pressure of the soil and any sharp objects present. In some cases, installing the insulated pipes within a protective duct can offer an additional layer of defense against soil pressure and potential damage, particularly for insulation types that are less robust.
British Standards and UK Regulations Governing pipe insulation for underground use
The installation and performance of underground pipe insulation in the UK are governed by a comprehensive set of British Standards and Building Regulations. These standards and regulations aim to ensure energy efficiency, safety, and the long-term reliability of pipework systems.
BS 5422 provides a method for specifying thermal insulating materials for pipes, tanks, vessels, ductwork, and equipment. It outlines key properties and performance criteria for various insulation materials, including thermal conductivity limits and allowable operating temperatures. BS 5970 offers a code of practice for the thermal insulation of pipework and equipment, recommending procedures for insulation in non-domestic and industrial facilities.
The Building Regulations Part L focuses on the conservation of fuel and power, setting standards for energy efficiency in buildings, including the insulation of heating and hot water pipes. This regulation specifies minimum insulation thicknesses based on pipe diameter and the thermal conductivity of the insulation material. Furthermore, the Water Regulations stipulate that all newly installed water pipes must be insulated before they are buried, providing guidance on protection against freezing.
For district heating systems, specific standards apply. BS EN 253 governs pre-insulated bonded pipe systems for directly buried hot water networks, covering the requirements and test methods for steel service pipes with polyurethane thermal insulation and a polyethylene outer casing. BS EN 15632 addresses pre-insulated flexible pipe systems used in district heating, outlining the classification, general requirements, and test methods for both bonded and non-bonded systems that utilize plastic or metal service pipes. PAS 67 is a Publicly Available Specification that provides best practice procedures for the installation of thermal insulating materials in buildings. The NHBC Standards also offer technical guidance on pipe insulation, including specific requirements for different areas within a dwelling.
Compliance with Approved Document L of the Building Regulations is essential for all construction projects in the UK. Additionally, local water authorities often have their own specific requirements regarding the insulation of buried water pipes, which must be adhered to. The comprehensive framework of British Standards, Building Regulations, and local authority requirements necessitates a thorough understanding of the specific context of each project to ensure full compliance and the delivery of efficient and reliable underground pipe systems.
Energy Efficiency and Cost-Saving Benefits
The use of effective underground pipe insulation in the UK yields significant energy efficiency gains and substantial cost savings over the lifespan of a system. Properly installed insulation can dramatically reduce heat loss from pipes, with some studies indicating reductions of up to 80%. Even insulating radiator feed pipes can lead to noticeable savings on heating bills, in the range of 2% to 5%. For larger systems, such as those in commercial buildings, applying insulation to cold water pipes can result in energy savings of up to 50%, while insulating hot water pipes can save up to 20% of energy costs.
These reductions in energy consumption directly translate to lower utility bills for both residential and commercial properties. Furthermore, in the UK's climate, the prevention of frozen pipes through effective insulation avoids the potentially high costs associated with repairs and water damage caused by bursting. The investment in pipe insulation is often recouped relatively quickly through the resulting energy savings, with payback periods potentially as short as a few years. While professional installation incurs a cost, homeowners with DIY skills can often install pipe insulation themselves at a very cost-effective rate, further enhancing the return on investment. It is important to note that while general percentages for energy savings are helpful, the actual savings achieved will depend on a variety of factors specific to each installation, including the local climate, the length and diameter of the pipes, the temperature of the fluid being transported, and the overall efficiency of the heating or cooling system.
In Summary;
-
Reduces heat loss from pipes by up to 80%
-
Insulating radiator feed pipes can save 2-5% on heating bills
-
For commercial buildings, insulating cold water pipes can save up to 50% of energy costs
-
Hot water pipe insulation can reduce energy use by up to 20%
-
Prevents costly repairs from frozen and burst pipes especially beneath concrete.
-
Typical payback periods range from 3-5 years for quality installations
Insulated Ducting for Underground Services
Beyond the insulation of individual pipes, insulated ducting plays a vital role in protecting various underground services in the UK, extending to applications beyond just fluid transport, such as housing electrical cables. The materials commonly used for underground ducting are typically plastics like HDPE (high-density polyethylene), LDPE (low-density polyethylene), PVC (polyvinyl chloride), and PP-R (polypropylene random copolymer), chosen for their durability and resistance to the often challenging ground conditions. For applications requiring enhanced strength, particularly in areas subject to heavy loads such as under roads, twinwall ducting is frequently employed, offering superior crush resistance.
The importance of insulation within underground ducting varies depending on the service being protected. For water pipes housed within a duct, insulation is primarily used to prevent freezing, maintain water temperature, and control condensation. The insulation materials used in these cases often include closed-cell foams like polyethylene. In the context of air ducts running underground, insulation serves to prevent condensation from forming within the ductwork and to reduce thermal losses or gains, ensuring efficient air distribution. Common insulation materials for air ducts include fiberglass, polyethylene foam, mineral wool, and phenolic foam, each offering different levels of thermal and acoustic performance.
Installation practices for underground insulated ducting in the UK are governed by specific regulations and utility company guidelines. The depth at which ducting must be buried varies depending on the type of service it contains (electricity, water, gas, communications) and its location (footpath, carriageway), with specified minimum depths to ensure safety and prevent damage. It is also crucial that ducts are sealed both internally and externally to prevent the ingress of gas, liquids, or vermin into buildings or the ducting itself. Plastic or rubber end caps are typically recommended for effectively sealing the ends of duct runs. Furthermore, the colour coding of underground ducting is a legal requirement in the UK, with different colours indicating the specific service contained within (e.g., blue for water, yellow for gas, black or red for electricity).
Ducting Materials and Applications
The materials commonly used for underground ducting are typically plastics like HDPE (high-density polyethylene), LDPE (low-density polyethylene), PVC (polyvinyl chloride), and PP-R (polypropylene random copolymer), chosen for their durability and resistance to challenging ground conditions. For applications requiring enhanced strength, particularly in areas subject to heavy loads such as under roads, twinwall ducting is frequently employed, offering superior crush resistance.
In the UK, colour coding of underground ducting is a legal requirement, with different colours indicating the specific service contained within (e.g., blue for water, yellow for gas, black or red for electricity).
Protective Measures for Compressible Materials
Insulated ducting serves a dual purpose for underground pipe insulation:
-
Protection from soil pressure: Prevents crushing of compressible insulation materials
-
Additional moisture barrier: Provides an extra layer of protection against groundwater
Common Challenges and Solutions with underground pipe lagging
Despite the numerous benefits, underground pipe insulation in the UK can present several challenges that need to be addressed through careful material selection and installation practices.
One of the most significant challenges is moisture ingress. Underground pipes are constantly exposed to moisture from the surrounding soil, which can degrade the performance of many insulation materials and lead to corrosion of metallic pipes. Compression of the insulation due to the pressure of the soil is another common issue, which can reduce the insulation's thickness and thus its effectiveness. Mechanical damage to the insulation or the pipes themselves can occur during the installation process or as a result of ground movement over time. In some areas of the UK, damage from rodents and other pests that might burrow underground and nest in or consume insulation materials can also be a problem. The natural thermal expansion and contraction of the pipes due to temperature fluctuations can also place stress on the insulation material, potentially leading to cracks or gaps. Improper installation, such as leaving gaps in the insulation or failing to adequately seal joints, is a frequent pitfall that can significantly compromise the insulation's overall performance. For metallic pipes, the combination of moisture and insulation can sometimes lead to corrosion under insulation (CUI), a hidden form of corrosion that can severely damage the pipe over time.
To mitigate these challenges, several solutions and best practices can be implemented. Using closed-cell insulation materials that inherently resist water absorption is a primary strategy. For insulation materials that are more susceptible to moisture, applying vapour barriers and waterproof jacketing can provide an effective shield against water ingress. Considering the use of pre-insulated pipe systems with a durable outer casing offers a robust solution that protects both the insulation and the carrier pipe. Installing the insulated pipes within a protective duct can provide an additional layer of defense against soil pressure and potential physical damage, especially for less robust insulation types. In areas prone to rodent problems, incorporating rodent-proof barriers can help prevent damage.
Ensuring proper installation with tightly sealed joints and continuous insulation coverage is fundamental to maximizing the insulation's effectiveness. For metallic pipes, selecting corrosion-resistant pipe materials or applying anti-corrosion layers before insulation can help to prevent CUI. Finally, ensuring proper bedding and backfilling around the pipes and insulation can provide necessary support and minimize the risk of mechanical damage from soil movement or sharp objects. Best Practices for Underground Pipe Insulation Installation
Successful underground pipe insulation installations depend on adherence to industry best practices and attention to technical details.
Trench Preparation
Proper trench preparation forms the foundation of effective underground pipe insulation:
-
Dig a trench deep enough to prevent freezing (depth varies by region and soil conditions)
-
Ensure trench width accommodates pipes and insulation with adequate spacing
-
Remove rocks, roots, and debris that could damage pipes or insulation
-
Provide a clean, compacted sand bedding of at least 10cm
-
Consider drainage needs for areas with high groundwater
Pipe Installation and Insulation
When installing insulated pipes underground:
-
Position flow pipes on the right-hand side looking from the heat source
-
Ensure proper spacing between pipes to maintain insulation integrity
-
Use appropriate joining methods (welding, compression fittings, etc.)
-
Insulate all connections and joints with the same level of protection as the main pipework
-
Test systems before backfilling to identify and address any leaks
Backfilling and Protection
The backfilling process is critical for protecting underground insulated pipes:
-
Apply initial layer of clean sand (minimum 10cm) directly around pipes
-
Compact carefully without damaging pipes or insulation
-
Place warning tape above pipework before completing backfill
-
Complete backfill with native soil, removing large stones
-
Ensure minimum coverage of 40cm above pipework
Moisture and Groundwater Considerations
For installations in areas with high groundwater tables:
-
"Lay the pre-insulated pipe system above the maximum groundwater level" where possible
-
For constant groundwater exposure, use special joint installation methods:
-
Electric welding of joints
-
Radiation cross-linked heat-shrink joints double sealed with adhesive and mastic
-
-
Consider increasing trench depth by 10cm to enable placement of a drainage course in impervious soils
Addressing Common Challenges
Several challenges specific to the UK context require careful consideration:
-
Moisture ingress: Use closed-cell materials like foamglass or elastomeric foam to prevent water absorption. In corrosive soils, additional PIB sheets or HDPE casings are recommended.
-
Rodent damage: Implement metal mesh barriers or crushed stone backfill to deter burrowing animals, a common issue in rural UK.
-
Frost heave: In Scotland and Northern England, burial below the frost line (1.5–2 m) is essential. For shallow trenches, rigid foam insulation above pipes can mitigate frost penetration.
-
Mechanical damage: Ensure proper bedding and backfilling around the insulated pipes to prevent damage from soil pressure and sharp objects.
-
Thermal expansion: Allow for pipe movement with proper spacing and flexible connections where needed.
Conclusion
Underground pipe insulation represents a critical component of energy-efficient and durable infrastructure throughout the UK. By selecting appropriate materials, following installation best practices, and adhering to relevant regulations, property owners and contractors can ensure optimal performance and longevity of underground pipe systems.
Whether using foam-based insulation, polyurethane, foamglass, or pre-insulated pipe systems, proper installation remains the key determinant of success. The higher initial investment in quality insulation and professional installation typically yields significant returns through energy savings, reduced maintenance requirements, and extended system lifespan.
As the UK continues to prioritise energy efficiency and infrastructure resilience, underground pipe insulation will remain an essential consideration for both new construction and renovation projects across residential, commercial, and industrial applications.
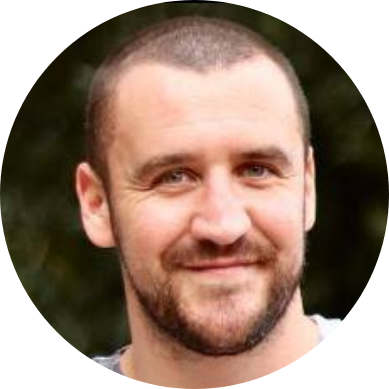
Samuel Hitch
Managing Director
Buy Insulation Online.
Leave A Reply
Your feedback is greatly appreciated, please comment on our content below. Your email address will not be published. Required fields are marked *