- Blogs
- What Is Trace Heating?
What Is Trace Heating?
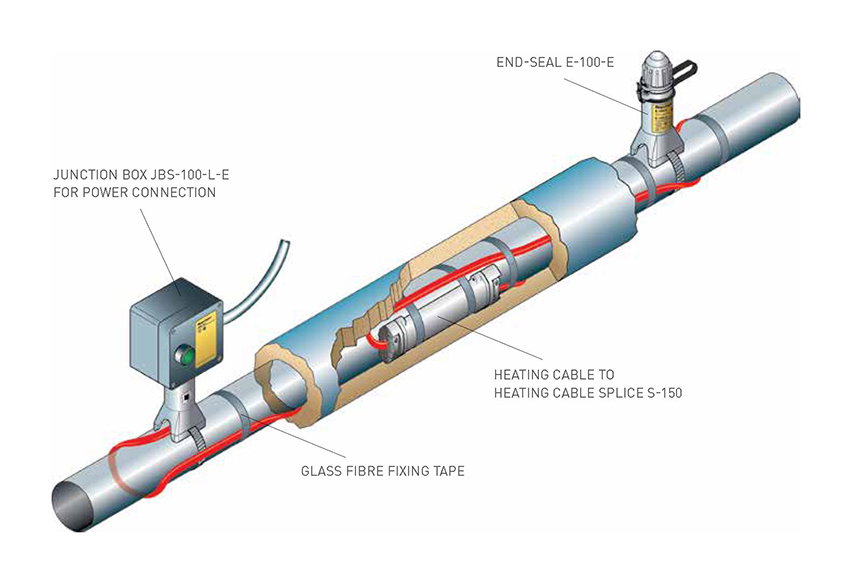
Trace heating is a type of technology used to keep pipes and other elements from freezing in cold temperatures. It's an important tool for any business or organisation that relies on plumbing and other systems to function properly.
Trace heating can be used in many situations, including commercial and residential buildings, as well as industrial and agricultural operations. In this article, we'll explore what trace heating is, its various applications, how trace heating works etc.
Principles Of Trace Heating ![]()
Trace heating is a solution for freezing pipes. Trace heating maintains the temperature above freezing point in process piping, tanks, and valves in industrial or commercial applications.
In simple terms, a heat trace system is where electrical cables or other heating elements are wrapped around the pipes or vessels supplying heat energy that is used to maintain or raise the temperature wherever required. Not only freezing, but heat trace also prevents heat loss from the pipe and helps maintain the temperature wherever required.
The trace heating system typically consists of several components, including a power source for supplying electricity to the cable, an insulation layer for protecting it from environmental effects, and a control system or thermostat, that regulates the temperature of the pipe or vessel.
To ensure optimal performance, trace heating systems should be designed based on specific application requirements such as climate conditions, physical characteristics of the pipe or vessel, and expected operational lifetime. Additionally, regular maintenance is necessary to ensure long-term operation and reliability.
Benefits Of Trace Heating
Trace heating is an effective way to maintain and prevent the temperature of pipes from dropping too low. It involves the use of electrical heating cables, which are designed to provide a continuous source of enough amount of heat to any surface they're laid on.
These cables can be used in a variety of applications, such as pipe tracing, roof and gutter de-icing, and tank heating. The benefits of trace heating far outweigh the costs associated with its installation and maintenance.
The primary benefit of trace heating is that it allows for better temperature control. By monitoring temperatures at different points along the cable's length, it's possible to maintain consistent temperatures over long periods of time - even when conditions change quickly or unexpectedly.
A trace heating cable is made to ensure that surfaces remain warm enough to protect against freezing or other potentially damaging conditions. Additionally, trace heating requires very little energy compared to other methods of temperature control, making it both cost-effective and environmentally friendly.
As the cables are laid beneath surfaces like pipes or tanks, they don't take up valuable space or visually interfere with the surrounding environment.
Another main benefit of trace heating is that it eliminates the need for expensive insulation, which can be costly and take up valuable space. Additionally, if the cables used are self-regulating trace heating they require minimal maintenance and can be easily monitored remotely, saving time and money on labour costs. In many cases, trace heating has been found to pay for itself within two years due to its energy efficiency.
Trace heating offers many advantages for those looking for reliable temperature control solutions in industrial and commercial settings alike. Its effectiveness at keeping surfaces warm without unnecessary energy consumption makes it an ideal choice for many applications where depending on external sources would be impractical or expensive.
Types Of Trace Heating
Trace heating is an essential process of thermal insulation for keeping pipes and tanks at a safe, uniform temperature. It's used in many industries to ensure the safety of personnel, equipment and the environment.
Without trace heating, water pipes and tanks can be exposed to extreme temperatures that can cause damage or even catastrophic failure. In this section, we'll look at the different types of trace heating available, so that you can make an informed decision about which type best suits your needs.
1. Electrical Trace Heating: Electrical trace heating involves using electric current to generate heat in the conductive element. The heating element is usually a resistance wire or a heating cable, which is placed along the length of the pipe or vessel to be heated.
2. Steam Trace Heating: Steam trace heating involves circulating steam through a pipe to heat it. The steam is usually generated in a boiler and then circulated through the pipe using a pump.
3. Hot Water Trace Heating: Hot water trace heating involves circulating hot water through a pipe to heat it. The hot water is usually generated in a boiler and then circulated through the pipe using a pump.
4. Self-Regulating Trace Heating: Self-regulating trace heating involves using a special type of heating cable that automatically adjusts its heat output based on the ambient temperature. This type of trace heating is ideal for applications where the temperature varies widely.
No matter what your application demands are, there’s sure to be a suitable heat tracing system available for your needs – you just need to know the correct trace heating system to your requirements and budget.
Types of Electric Trace Heating Cables: ![]()
Electric trace heating cables are typically of two main types:
-
Constant Wattage Heating Cables: Constant wattage trace heating cables have a uniform heating output along the entire length of the cable. They are designed for applications where the ambient temperature remains relatively constant, and a constant heat output is required. Constant wattage heating cables are available in different wattages and voltages, depending on the specific application.
-
Self-Regulating Heating Cables: Self-regulating trace heating cables are designed to automatically adjust their heat output based on the ambient temperature. These cables are constructed of conductive polymer material that contracts and expands as the temperature changes. This contraction and expansion regulate the heat output of the cable. Self-regulating heating cables are ideal for applications where the ambient temperature fluctuates widely, such as in outdoor environments.
Trace Heating Applications
As mentioned before, trace heating systems are used to keep tanks, vessels, and other equipment warm enough to function properly.
Trace heating is also suitable for use in hazardous environments since it does not rely on combustible fuels like oil or gas for its operation.
Trace heating systems have been widely adopted across a variety of industries including utilities, manufacturing facilities, food processing plants, and even healthcare settings where there's an increased risk of freezing temperatures and equipment failure.
Some of the common applications of trace heating include:
-
Freeze Protection: Trace heating is used to prevent the freezing of water and other fluids in pipes and tanks, which can cause damage to the equipment and disrupt the flow of the process. Freeze protection is commonly used in cold climates or where outdoor temperatures drop below freezing.
-
Process Temperature Maintenance: Trace heating is used used to protect pipes from heat loss and maintain the temperature of process fluids in pipelines, tanks, and vessels, ensuring that the process operates at optimal temperatures for consistent quality and safety.
-
Hot Water Temperature Maintenance: Trace heating is used to maintain the temperature of hot water systems in buildings, ensuring that hot water is always available for domestic and industrial use.
Installation Considerations For Heat Trace ![]()
Trace heating is the process of design and installation of electrical heat tracing cables along a pipe or duct to maintain a constant temperature. It is typically used in areas where temperatures are prone to freezing and can cause problems if not managed properly.
Prior to installation, it is important to consider the type of conditions that will be encountered, such as high humidity or corrosive atmospheres. The physical environment including any potential obstructions around the piping and ductwork, as well as any adjacent components that may interfere with electrical wiring should also be considered
Additionally, the voltage requirements or power output required for the system should be determined, depending on the application's needs. Any insulation needed for protecting against heat loss should also be taken into account for optimal performance.
Furthermore, it is important to ensure that all connections are secure and rated appropriately for safety and efficacy. All these factors should be weighed before installation begins so that there are no issues during operation.
In order to maximise efficiency and minimise energy costs, proper sizing of the trace heating system is essential. This includes determining the length of the cable required, the power output of the cable, choosing an appropriate wattage rating, and selecting a suitable voltage level.
The layout of the system should also be planned carefully in order to optimise its performance over time. It is important to follow all manufacturer's instructions for proper installation and maintenance for optimal results from trace heating systems.
Frequently Asked Questions
How to Maintain A Heat Trace System?
Maintenance for electric trace heating is essential to ensure it continues to operate efficiently and safely. This includes regularly inspecting the system for any damages, such as loose connections or exposed wires, faults somewhere along the cable installed, and making sure that all safety devices are functioning properly.
Additionally, it's important to inspect the insulation in the trace heating system and repair any areas that have been damaged. It's also a good idea to periodically check the power supply to ensure it's providing enough voltage to support the trace heating system.
What Are The Safety Risks Associated With Trace Heating?
Trace heating poses potential safety risks for those who use and install it. Improper installation and maintenance can lead to exposed electrical wiring, which can cause electric shock or fires.
Additionally, excess heat build-up from faulty trace heating systems may cause property damage, as well as burns and other injuries if touched. Therefore, it is important to take the proper precautions when installing trace heating systems and regularly inspect them for any signs of wear or damage.
What Is The Cost Of Trace Heating?
The cost of trace heating in the UK varies depending on various factors such as the type of trace heating system, the length of the pipeline or equipment to be heated, and the installation and maintenance costs.
For example, the cost of electrical trace heating cables can range from £3-£15 per linear meter, while the cost of steam trace heating can range from £20-£50 per linear meter. However, the installation costs can add up depending on the complexity of the installation process, and the cost of labour in the region.
In general, the cost of trace heating in the UK can range from a few hundred to several thousand pounds, depending on the specific requirements of the application. It's recommended to consult with a qualified trace heating specialist or supplier to get an accurate cost estimate based on the specific needs of the project.
How Long Does Trace Heating Last?
Trace heating can last for years, depending on the type of material used, its quality and installation. High-quality Electric Resistance Heating (ERH) systems are designed to last an average of 10-15 years, while Self-Regulating Heating Cables (SRHCs) typically last up to 25 years.
Is Trace Heating Suitable For All Types Of Pipework?
Trace heating is suitable for all types of piping, as it provides a reliable and consistent source of heat. It is an effective solution for both low and high temperatures, helping to prevent freezing and overheating of pipes in extreme conditions. Trace heating can be used on metal, plastic, or composite pipe materials, making it a versatile option that can be tailored to meet the needs of any project.
Conclusion:
Trace heating is an effective way to maintain temperatures in pipes, especially in cold climates. It's important to be aware of any safety risks associated with trace heating and take the necessary precautions.
The cost of trace heating can vary depending on the type of piping and size of the project, but it typically lasts for several years. Depending on the application, trace heating may not be suitable for all types of piping.
Ultimately, investing in trace heating could save you money and time in the long run. We'd recommend researching to identify the correct trace heating before taking any action.
For all your trace heating requirements, visit Buy Insulation Online. Along with trace heating cables, we also stock junction boxes, tapes and all that you need to complete your trace heating installations. In addition, we also stock pipe insulation, cladding, valve covers and other products that could also be used along with trace heating.
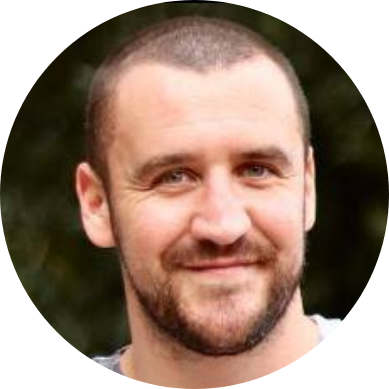
Samuel Hitch
Managing Director
Buy Insulation Online.
Leave A Reply
Your feedback is greatly appreciated, please comment on our content below. Your email address will not be published. Required fields are marked *